Encoder Couplings
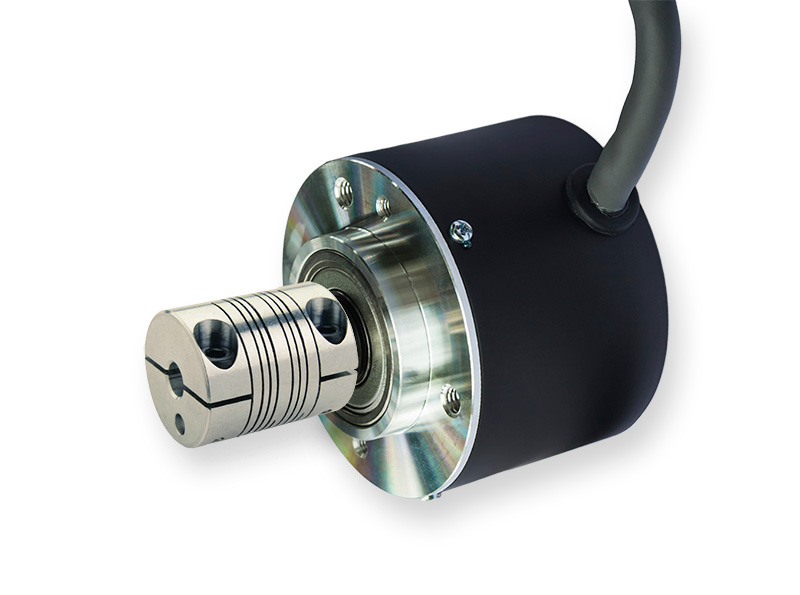
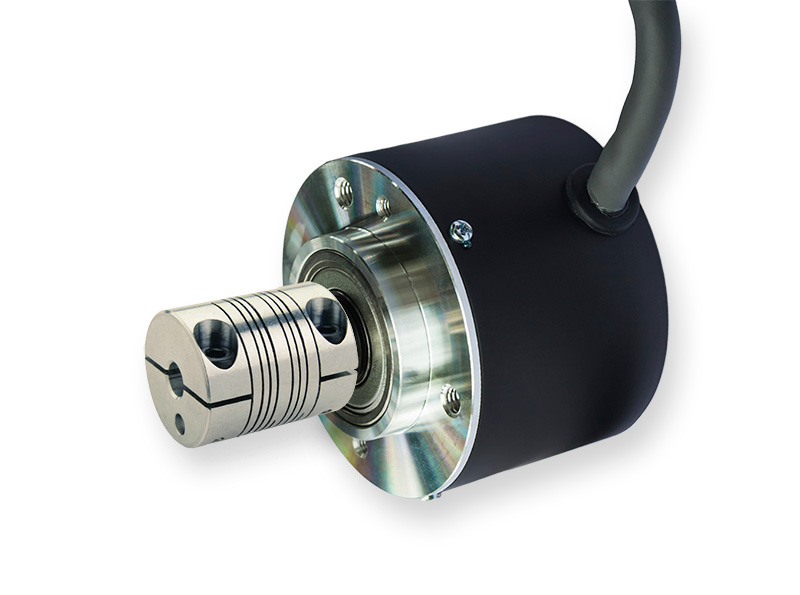
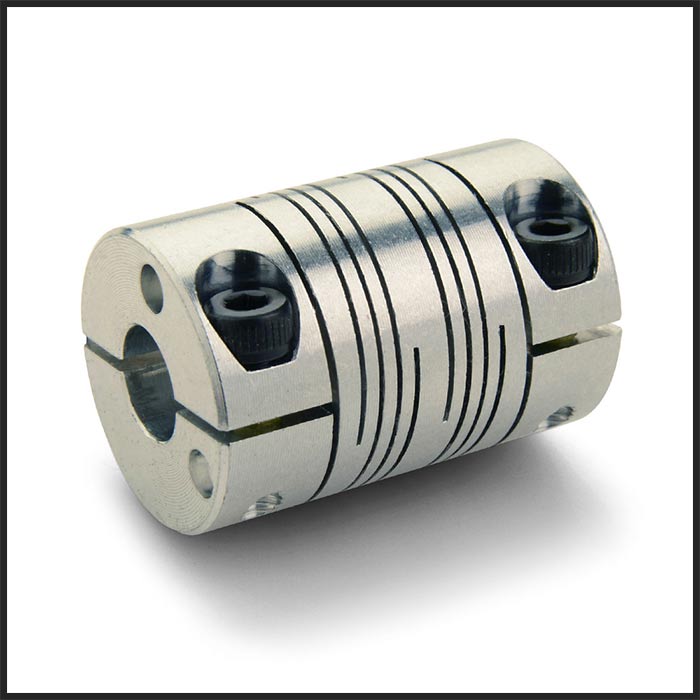
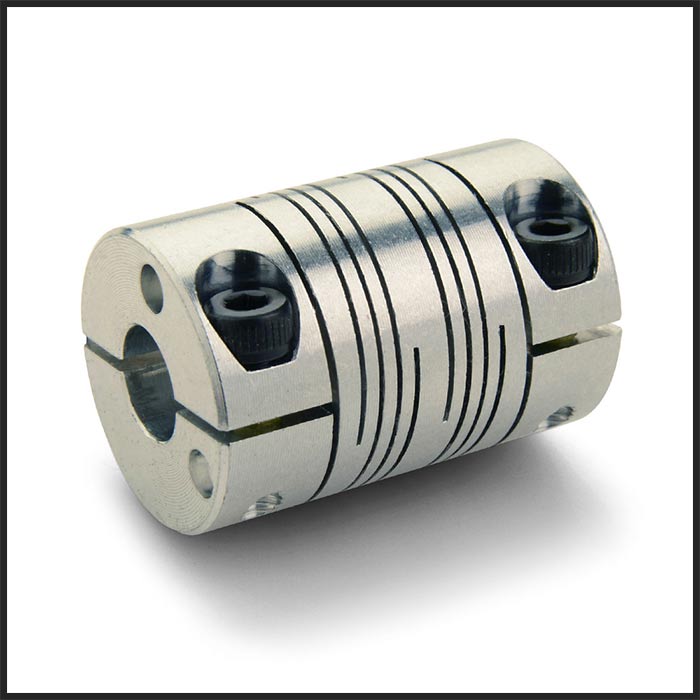
+ Zero-backlash operation
+ High angular misalignement
+ Aluminum for low inertia
+ P- and MW-series for compact lengths
+ Balanced design for speeds up to 6,000 RPM
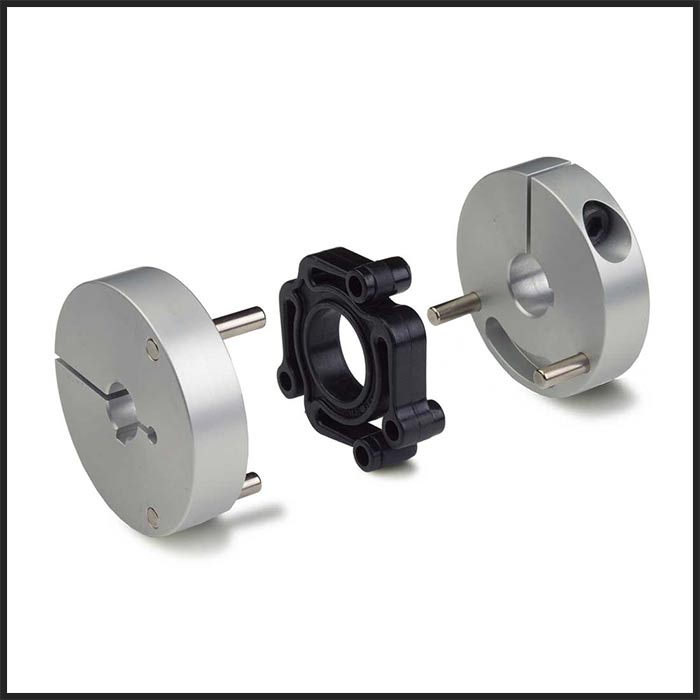
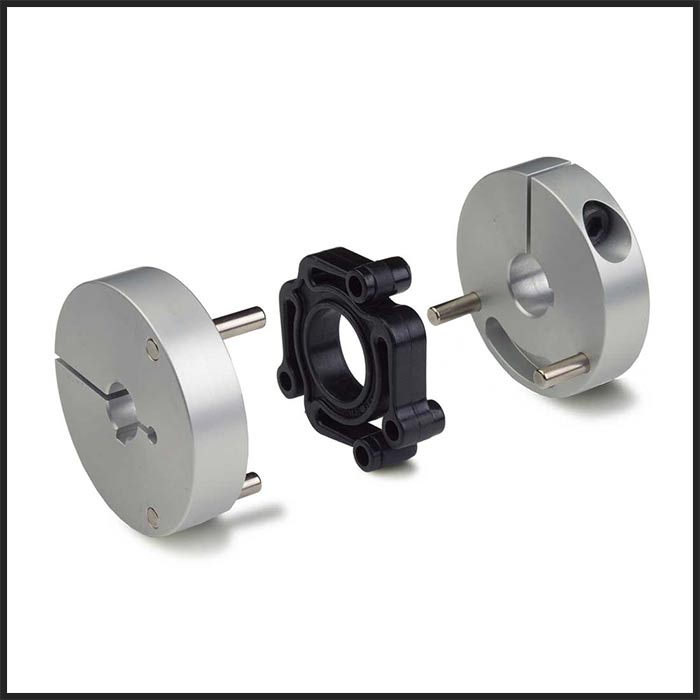
+ Zero-backlash operation
+ Single insert style for compact installations
+ Double insert style for longer lengths
+ Widest range of bore sizes
+ Lowest bearing loads
+ Best all around misalignment capabilities
+ Balanced design for speeds up to 25,000 RPM
How To Select A Coupling For Your Encoder System
We have seen it all when it comes to encoder "couplings" - duct tape, flexible plastic tubing, etc... These bush fixes are often required due to poor coupling selection during the design stage of the system. In many cases, the inconvenienced end user was not the system designer, however they are left to find a less than ideal solution since the system was not designed using standard widely available components. Selecting a coupling early in the design cycle that matches all system requirements leads to reduced costs for the end user and original manufacturer, reduced frustration in trying to source replacements, and increased performance. The encoder system designer will need to consider speed, inertia, misalignment, operating environment, and envelope when specifying the coupling.
P- and MW-Series beam couplings are designed to be torsionally stiffer with less wind-up than commodity style beam encoder couplings found elsewhere on the market, giving them increased performance and accuracy. Ruland beam couplings are manufactured with a multiple cut design to accommodate all forms of misalignment, especially parallel which is limited in commodity encoder couplings. Beam couplings from Ruland are available in 7075 aluminum for light weight and low inertia. Stainless steel options are also available, although the added mass of stainless steel makes it less ideal in most encoder applications. The user will also have to change hardware if using in a corrosive application as hardware is supplied in alloy steel.
Beam couplings have a proven track record of success in encoders and are a solid place to start when designing an encoder system. Beam couplings really shine in applications with high angular misalignment and this extra flexibility helps to reduce bearings loads, which is critical in encoders with small sensitive bearings.
Designed specifically for encoders, Controlflex couplings offer designers flexibility in standard sizing options, misalignment accommodation, and RPM capabilities that other encoder couplings do not offer. Controlflex couplings are a zero-backlash design comprised of two lightweight aluminum hubs and either one or two center inserts. The lightweight balanced design allows for speeds up to 25,000 RPM depending on the OD size of the hub. The use of one or two inserts allows the designer or user to match length and performance to the needs of the encoder system. Hubs are available in standard and reduced widths to accommodate various installation envelopes. Controlflex couplings have a wide range of bore sizes in a given outer diameter with ratios of large to small bore over 3:1, which is particularly useful in encoders where the motor shaft can be more than twice the size than that of the encoder.
Controlflex couplings are designed with the center insert as the wear element. The insert concentrates forces onto their flexible limbs allowing for accommodation of all forms of misalignment and reduced bearing loads, which is critical in encoders that often have small sensitive bearings. Controlflex couplings have the best all around misalignment characteristics. This is useful in encoder systems as misalignment is often not tightly controlled and all forms may be present.
Oldham couplings offer designers zero-backlash operation, low mass and inertia, low bearing loads, and a balanced design for reduced vibration in encoder applications with RPM up to 4500. Oldham couplings are characterized most by their high parallel misalignment accommodation, which reaches up to 10% of the coupling OD. They also have the advantage of multiple hub and insert materials, which are interchangeable based on application needs. Aluminum hubs are ideal for most encoders where lightweight is desired. Stainless steel hubs are a good option for corrosive environments such as food processing where the coupling will be directly exposed to the operating environment. All hubs are available in clamp and set screw style with or without keyways in inch or metric bore configurations giving designers a high amount of flexibility when designing an oldham coupling into their encoder application. Disks are available in three materials including acetal for high torque and general purpose use, nylon for dampening, or PEEK for high temperature and low out gassing.